The Essential Role of Lathing Parts in Modern Metal Fabrication
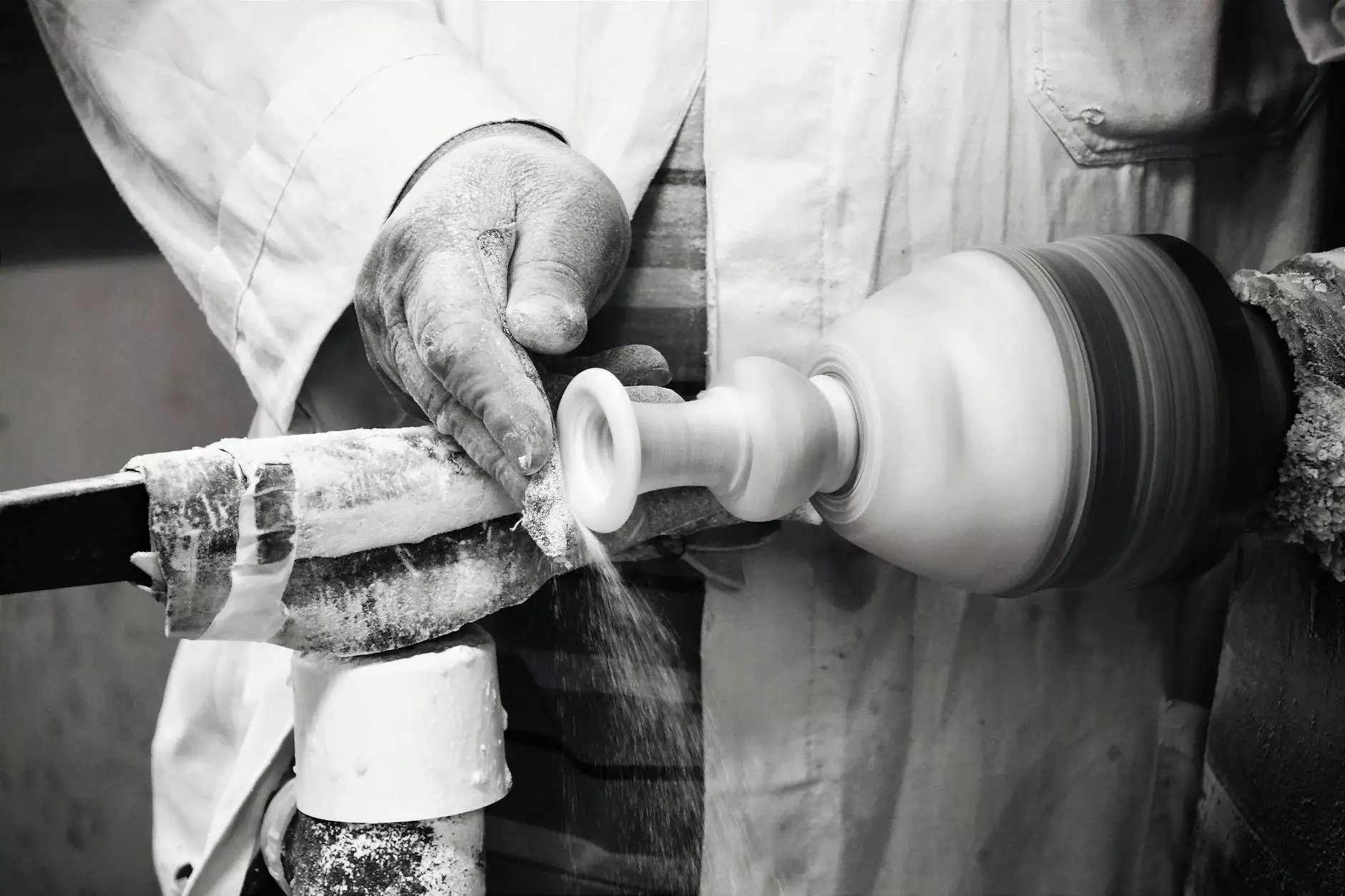
Lathing parts play a crucial role in the world of metal fabrication, serving as foundational components in various industries ranging from automotive to aerospace. The precision and quality of these parts directly impact the functionality and durability of the final products. In this article, we will explore what lathing parts are, their manufacturing processes, applications, and how they contribute to the success of businesses like deepmould.net.
What Are Lathing Parts?
Lathing parts refer to components that are produced through the lathe machining process, where material is removed from a rotating workpiece to create cylindrical shapes and intricate designs. This technique is essential for achieving high precision and producing complex geometrical features. During the lathing process, a cutting tool removes material from the workpiece, allowing for the creation of parts with tight tolerances and excellent surface finishes.
The Importance of Lathing Parts in Metal Fabrication
In the metal fabricators’ industry, lathing parts carry significant weight due to several factors:
- Precision Engineering: Lathing allows for the creation of highly accurate and consistent parts, which is vital in industries that require strict adherence to specifications.
- Versatility: The lathing process can be adapted to a wide variety of materials, including metals such as aluminum, brass, steel, and composites.
- Cost-Effectiveness: With advancements in technology, automated lathes and CNC programming have reduced production costs while increasing efficiency and productivity.
Types of Lathing Parts
Lathing parts can vary greatly in type and use. Some common examples include:
- Shafts: Crucial components for machines that transmit power and motion.
- Housings: Enclosures that protect other mechanical components.
- Bushings and Bearings: Components that reduce friction and enable smooth movement.
- Fittings and Adapters: Essential for connecting different parts of machinery and equipment.
The Lathing Process Explained
The lathing process can be broken down into several key steps:
1. Design and Planning
The first step involves creating a detailed design of the part to be lathed, considering dimensions, tolerances, and material specifications.
2. Selecting the Material
Choosing the right material is critical. Depending on the application, different metals and alloys may be selected for their specific properties, such as hardness, corrosion resistance, and machinability.
3. Setting Up the Lathe
CNC lathes have revolutionized the manufacturing process, allowing for automated precision cutting. Programmers input the design specifications directly into the system, ensuring every cut is executed with accuracy.
4. Machining the Part
With the setup complete, the lathe begins the machining process. The workpiece is secured, and the cutting tool operates at programmed speeds to shape the metal.
5. Finishing and Quality Control
Once the lathing is complete, finishing processes such as polishing, grinding, or anodizing may be employed to enhance the surface quality. Quality control checks are performed to ensure each part meets the precise specifications set out in the design.
Applications of Lathing Parts Across Industries
Lathing parts find applications in numerous sectors. Some notable areas include:
1. Automotive Industry
In automotive manufacturing, lathing parts such as gear shafts, brake rotors, and engine components must meet stringent quality standards to ensure durability and safety.
2. Aerospace Sector
The aerospace industry often requires lathing parts to be made from lightweight, high-strength materials. Components like turbine housings and landing gear elements depend on precise lathing operations for performance and safety.
3. Medical Devices
Medical technology often employs lathing parts to create essential equipment such as surgical instruments, which demand a high level of precision and hygiene.
4. Manufacturing Equipment
Manufacturing machinery itself utilizes lathing parts, including rotary tables and spindle assemblies, that require impeccable engineering to ensure efficient operation.
Choosing the Right Partner for Lathing Parts
When seeking high-quality lathing parts, it is essential to choose a reputable metal fabricator. Here’s why deepmould.net stands out:
- Advanced Technology: Utilizing the latest CNC lathes to deliver high precision and efficiency.
- Expertise and Experience: A team of skilled engineers and machinists dedicated to quality and innovation.
- Comprehensive Services: Offering full-service solutions, from design and prototyping to production and finishing.
Innovative Techniques in Lathing Parts Production
The field of lathing is continuously evolving, with new techniques improving efficiency and outcomes. Some innovative processes include:
1. CNC Machining
Computer Numerical Control (CNC) has transformed lathing by allowing for precise and repeatable cuts with minimal human intervention. This increases production rates and reduces errors.
2. Multi-Axis Lathes
These lathes can operate on multiple axes simultaneously, enabling the production of complex parts in one setup, thus saving time and increasing precision.
3. Additive Manufacturing Integration
In some cases, integrating lathing with additive manufacturing (3D printing) allows for the production of parts that require both additive and subtractive techniques, leading to innovative designs.
Best Practices for Quality Lathing Parts Production
To ensure the highest quality lathing parts, manufacturers should adhere to the following best practices:
- Regular Maintenance: Keeping lathes and tooling in excellent condition to avoid defects.
- Skilled Workforce: Continually training employees to maintain high competency in operating machinery and understanding design specifications.
- Robust Quality Control: Implementing strict inspection protocols throughout the manufacturing process to catch issues early.
The Future of Lathing Parts in Metal Fabrication
As technology continues to advance, the future of lathing parts looks promising. With increasing demands for precision and efficiency, the integration of smart manufacturing processes will likely enhance quality and reduce waste."
Moreover, industries are consistently pushing the boundaries of what’s possible with lathing, leading to new applications and innovations that can further optimize production and part performance.
Conclusion
In conclusion, lathing parts are more than just components; they are essential elements that power various industries in today's economy. Understanding their production, applications, and the implications on quality and efficiency is crucial for businesses striving for success in metal fabrication.
With experts like deepmould.net leading the charge in quality and precision, companies can rest assured knowing their lathing parts are produced to the highest standards. Embrace the potential of lathing parts and enhance your products with unrivaled precision!