Understanding Injection Molding and Its Local Benefits
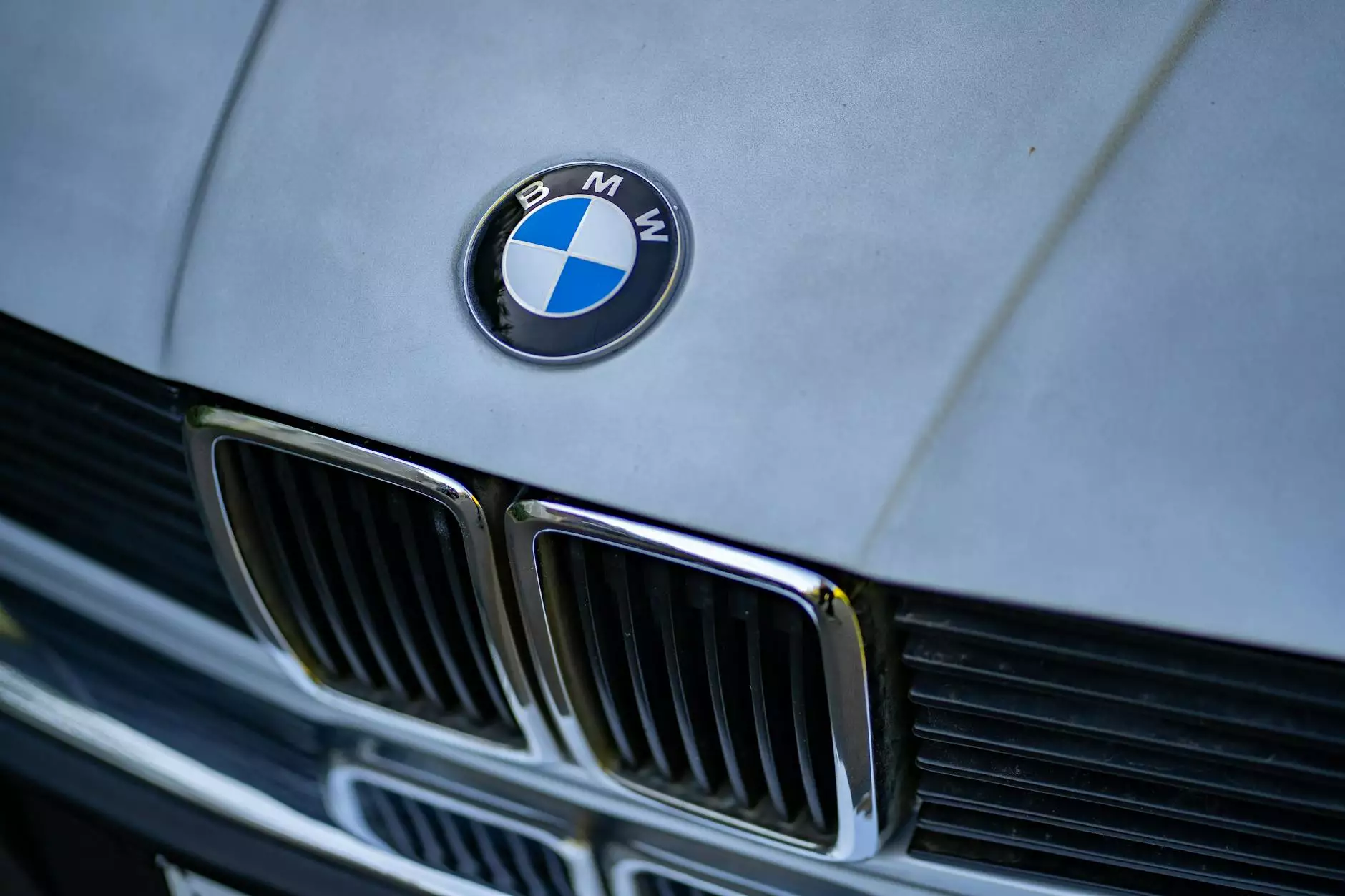
In today's fast-paced industrial landscape, finding a reliable partner for your manufacturing needs is crucial. If you are searching for injection molding near me, you're on the right path to enhancing your production capabilities. This article will delve into the intricacies of injection molding, focusing on its applications, particularly in the electronics and medical supplies sectors.
What is Injection Molding?
Injection molding is a highly efficient manufacturing process used for producing parts by injecting material into a mold. This method is particularly favored for its ability to create large volumes of identical parts with precision and minimal waste. The materials commonly used in injection molding include plastics, metals, and glass.
The Advantages of Injection Molding
- High Production Rate: Injection molding is capable of producing thousands of parts per hour, making it extremely efficient for large production runs.
- Cost-Effective: Once the initial setup is complete, the cost per unit decreases significantly with high production volumes.
- Complex Shapes: Injection molding allows for intricate designs that would be impossible to create with traditional manufacturing methods.
- Material Versatility: It supports a wide range of materials, including thermoplastics and thermosetting plastics, which can be tailored to specific applications.
- Consistency in Quality: Injection molding ensures uniformity in product quality, crucial for industries such as electronics and medical supplies.
Injection Molding in the Electronics Sector
The electronics industry often requires precise components that not only fit perfectly but also withstand varying environmental conditions. Here’s how injection molding excels in this field:
Precision and Quality
When manufacturing electronics components, precision is key. Injection molding enables manufacturers to achieve tightly controlled tolerances, ensuring that each part meets the strict specifications required for electronic components.
Material Options
The variety of materials available for injection molding includes engineering plastics such as polycarbonate and ABS, which are ideal for electronics due to their strength, durability, and electrical insulating properties.
Customization
With injection molding, businesses can create customized components that perfectly fit their devices. This flexibility allows for innovation in product design, helping companies to stand out in a competitive market.
Injection Molding in Medical Supplies
As the demand for medical supplies grows, so does the need for reliable and efficient manufacturing processes. Injection molding plays a pivotal role in this industry as well:
Compliance and Safety
The medical industry is heavily regulated, and products must meet stringent quality standards. Injection molding allows for consistent quality control practices, making it easier to comply with regulations from organizations like the FDA.
Production of Complex Geometries
Medical devices often have complex geometries and require high levels of precision for functionality. Injection molding is uniquely suited for this because it can produce detailed designs that enhance the performance of medical supplies.
Bulk Manufacturing
Injection molding is ideal for bulk manufacturing, which is essential in the medical field, where devices such as syringes, surgical tools, and diagnostic devices need to be produced in large quantities to meet healthcare demands.
Finding Injection Molding Services Near You
When looking for injection molding near me, it's essential to consider several factors to ensure that you partner with the right manufacturer:
Experience and Expertise
Choosing a provider with a proven track record in injection molding, especially within your industry, is crucial. Look for companies like Nolato, renowned for their expertise in electronics and medical supplies, ensuring high standards and innovation.
Technology and Equipment
State-of-the-art equipment can make a significant difference in the quality of molded parts. Ensure your chosen facility has modern machinery capable of handling your production needs efficiently and effectively.
Customer Support
Effective communication and support throughout the manufacturing process can alleviate many headaches. Your provider should be accessible and willing to help you with any concerns or questions you may have.
The Future of Injection Molding
As technology advances, so too does the field of injection molding. Here are some trends that are shaping the future of this manufacturing process:
- Automation: Increasing automation in the injection molding process enhances efficiency and reduces labor costs.
- 3D Printing Integration: The incorporation of 3D printing technologies is beginning to influence injection molding, allowing for faster prototyping and shorter lead times.
- Advanced Materials: Development of new materials that offer improved performance characteristics will open further avenues for application in various sectors, including electronics and medical devices.
- Environmental Concerns: The industry is increasingly focusing on sustainable practices, such as recycling plastics and reducing the carbon footprint of manufacturing processes.
Conclusion
Injection molding remains a cornerstone of modern manufacturing, especially for the electronics and medical supplies industries. By choosing local services for injection molding near me, businesses can leverage the benefits of quality production, fast turnaround, and reduced logistics costs. Companies like Nolato exemplify the capabilities you should look for in a manufacturing partner, providing world-class solutions to meet your precise needs.
In summary, embracing injection molding for your manufacturing needs can lead to unparalleled advantages in quality, efficiency, and innovation. As the industry evolves, staying informed about the latest advancements will be crucial for maintaining a competitive edge. If you are in the market for injection molding, the time to act is now.